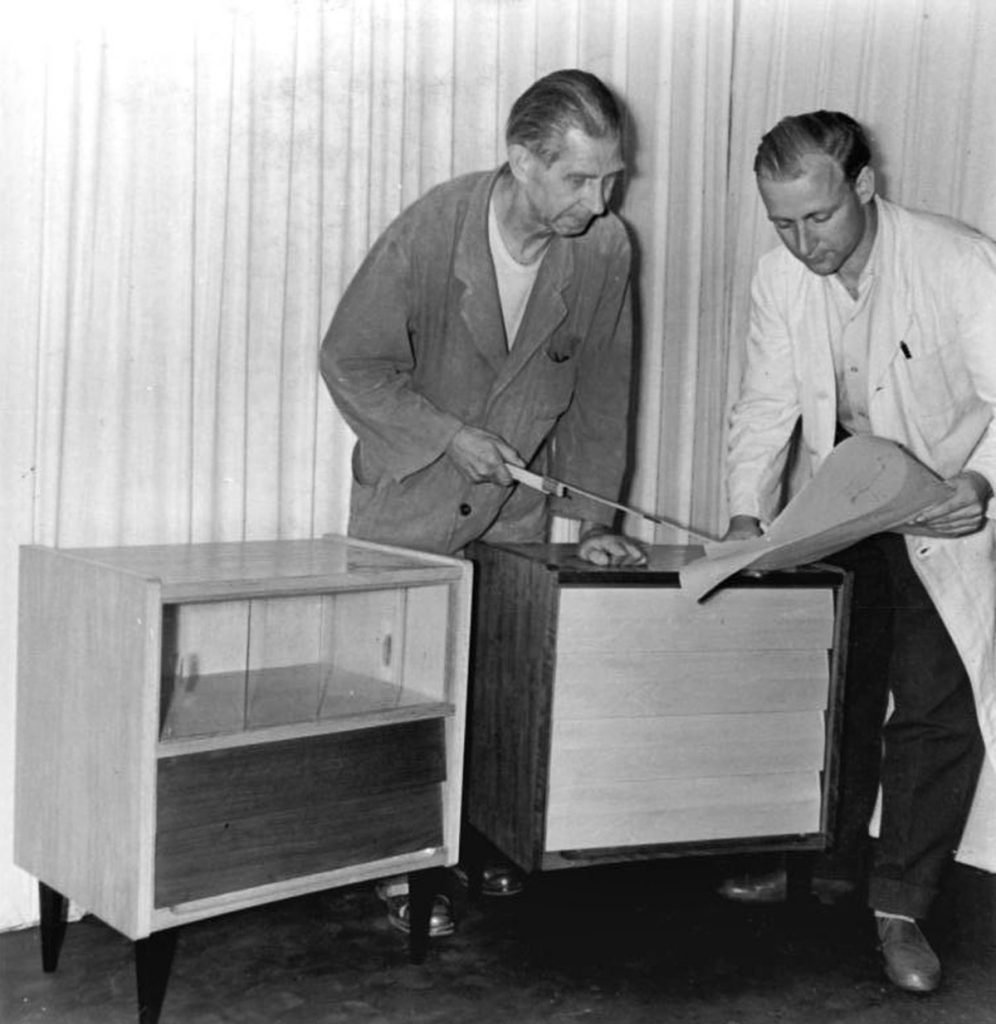
Möbel aus Friedrichshain.
Von
Am 12. Juli 1950 jubelte die SED-Tageszeitung Neue Deutschland: „Im VEB Berliner Möbelwerke fliegen die Späne“. Intern jedoch musste Friedrich Gajewski, parteilos und Leiter der Arbeitsvorbereitung zugeben: „Wir sind durch den außerplanmäßigen Auftrag der 400 Konferenztische in diesem Monat stark überlastet”. Die Konferenztische – der außerplanmäßige Auftrag – waren für den III. Parteitag der SED bestimmt. Gajewski hatte ein Problem: die „fliegenden Späne“ waren zu dick. Er brauchte dünne Späne. Davon hatte er zu wenige. Der „VEB Berolina Möbelfabrik“ sammelte Holzspäne für Pressplatten. Nur, Holzspäne mussten beim „VEB Feinwurst“ abgegeben werden. Ständig wurden Buchenholz und andere Späne für die Räucherei benötigt, die dem Berolina Möbelwerk fehlten. Die „Berliner Möbelwerke“, an der Warschauer Straße 58 verfügten über effektive Vierblattkreissägen, die wenig Abfall erzeugten. Traurig berichtete Herr Gajewski: „Es entsteht ein ganz geringer Anfall von Holz- und Späneabfällen, zudem kommen über die Absaugvorrichtung des gesamten Betriebes zu wenige Hobelspäne zusammen. Diese Menge wie auch die Mischung taugt nicht zur Produktion von Pressplatten“.
Ersatz
Echtes Tischlerholz, war 1951 Mangelware. „Isotrope richtungslose Holzspanplatten“, aus zerspanten, fest gepressten und verklebten Holzabfällen sollten diesen Mangel beseitigen. Erfolgreich verarbeitete die Westdeutsche Firma Otto Kreinbaum Presspäne für ihre „Okaltüren“. Um einschlägige Schriften einzusehen, ging ein Möbelwerker ins Westberliner Patentamt. Der dafür nötige Idealspan sollte 0,5 mm Stärke und 1 – 2 Kubikzentimeter Fläche haben. Welche Bindemittel, welche Drücke und Temperaturen zum Einsatz kommen sollten, wurde bei den DDR-Hohlsteinziegeleien und Papierfabriken angefragt. Das VEB Plattenwerk Schönheide hatte herausgefunden, dass sich Hobelspäne gut verarbeiten ließen, wenn sie in einem Nebel aus „Thermocolleim“ besprüht werden. Das Spänegut ständig mit Harken und Schaufeln umzuwenden, war Frauenarbeit. Die klebrigen Späne wurden dann in einen Spänekasten geschüttelt und von diesem in eine Zinklauge, wo sie teigartig zusammenbackten. Dieser „Teig“ kam zur Plattenpresse. 10 Atü Druck bei 300 Grad Temperatur waren mit dieser Presse aus Westproduktion möglich. Aus volkseigener Produktion gab es solche nicht. Auch vom „Thermocolleim“ war zunächst nicht viel vorhanden. Die Spanplattenproduktion nach diesem Verfahren sollte helfen, viele Möbel und andere Holzerzeugnisse herzustellen. Da geeignete Späne aber zur Mangelware zählten, durfte 1952 das Sägewerk Stralau Holzreste nicht mehr gegen Küchenabfälle tauschen. Damit fehlten den Viehzüchtern die Küchenabfälle für ihre Schweine und Kühe.

Erfolge
1954 wurden monatlich 400 Schlafzimmer hergestellt. Der Polier Wischer sagte: „Wir sind bestrebt, stets gute Möbel anzufertigen, denn sie werden ja von Arbeitern gekauft”. Das Modell „Erika“, aus Eiche, mit Birke abgesetzt, mit einem 1,80 Meter breiten Schrank. Dann „Dagmar” und „Helga”, beide mit einem 2,20 Meter-Schrank. Und in Birke – die „Rita”, mit 2.2 Meter- Schrank plus Herrenkommode. Da am 17. August 1954 im Neuen Deutschland stand: ‚Die Bäume wachsen nicht wie Kartoffeln‘, gab Nationalpreisträger Professor Diplom- Ingenieur Stanek die Parole heraus: “Jede klar formulierte Aufgabe enthält bereits 50 % ihrer Lösung“. Die Leuna-Werke „Walter Ulbricht“ entwickelten den farblosen Kunstharzleim 602 / 40. Der ließ sich gut versprühen und härtete bei 90 – 100 Grad aus. In kleinen Formaten war damit eine Produktion volkseigener Spanplatten möglich und das Transparent „1955, das Jahr der Spanplatte“ zierte die Werkstätten der Möbelwerker. 1956 hieß das Ziel: 4.600 Schlafzimmer aus „Sauerkohlplatten“, allein 600 vom Model „Helga“. Stolz brachten die Möbelwerker „Helga“ „Rita“ und „Dagmar“ zur Leipziger Messe. Die westdeutsche Fachzeitschrift „Möbel-Kultur“ urteilte in Heft 11: „Der Durchbruch zur industriellen Fertigung, wie wir sie seit Jahren kennen, zeichnet sich nun auch in Ostdeutschland stellenweise in klaren Konturen ab. Im Allgemeinen dominiert die dem alten Kulturerbe entlehnte gutbürgerliche Einrichtung“.
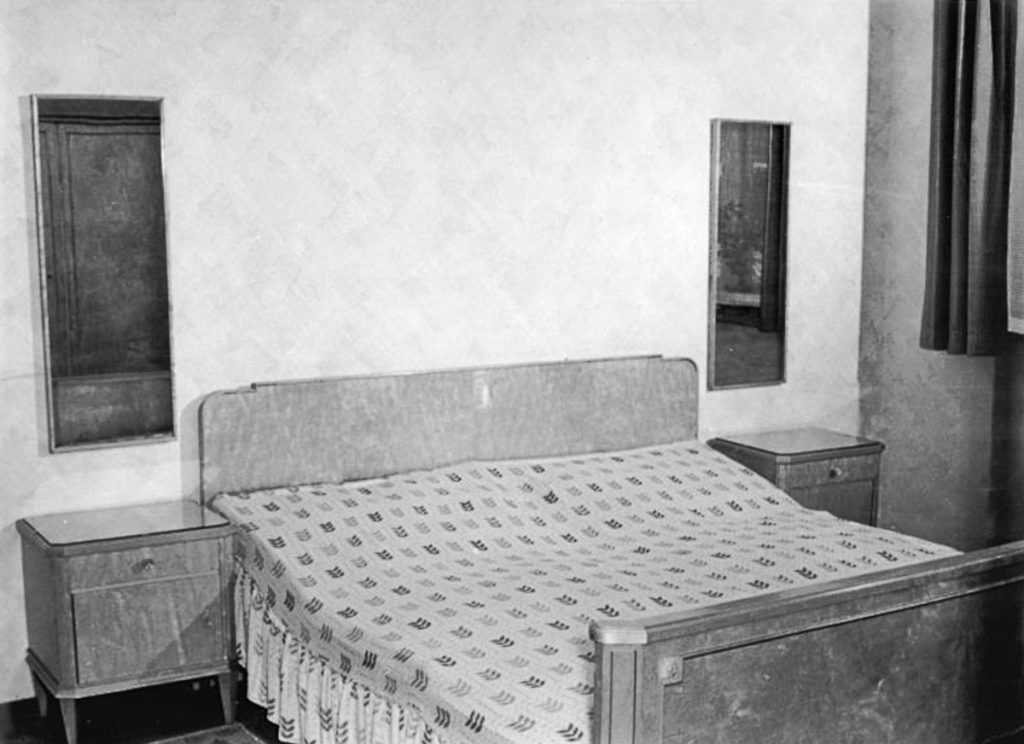
Vor Ort
Die staatliche Berliner Möbelindustrie erzielte Abschlüsse über vier Millionen Mark, davon eine Million für den Export und wurde wegen ihrer „Abkehr vom Altherkömmlichen“ vom „Ministerium für Leichtindustrie“ gelobt. Freude darüber kam im Möbelwerk nicht auf. Zur Elektrizitäts- und Dampfversorgung stand nur ein stationärer Lokomotivkessel Jahrgang 1937 und ein Siederohrkessel Jahrgang 1902 zur Verfügung. Alle anderen Maschinen hatten Schrottwert. Sie stammten aus der Vorkriegszeit. Ein Gutachter sagte, die Fertigungsweise der 176 Produktionsarbeiter wäre „handwerklich, diskontinuierlich und von schlechten Lichtverhältnissen beeinträchtigt. Infolge des hohen Krankenstandes fehlten ständig Arbeitskräfte. Wegen der hohen Selbstkosten wäre eine Angleichung an das Weltmarktniveau ausgeschlossen“.
Umzug
Im Oktober und November 1960 wurden ersten Planungen und ein Finanzierungsplan für ein neues Berliner Möbelwerk in Karlshorst erstellt. Die städtebauliche Forderung lautete: „Entfernung der Produktionsbetriebe aus dichtbesiedelten Wohngebieten“. Das neue Werk sollte zwischen 1961 und 1962 entstehen. Allerdings, ein erheblicher Teil der neuen Maschinen wie der sonstigen Ausrüstung waren Importe aus dem Westen. Im Zuge der „Störfreimachung“, einer Kampagne, konstruktive Alternativen für den Fall zu entwickeln, dass nach dem Mauerbau keine Ersatzteile mehr aus dem Westen zu haben waren, stoppte der Ausbau des Karlshorster Werkes. Erst im April 1964 hieß es offiziell: „Berlins modernste Möbelfabrik in Karlshorst soll Anfang Juni produzieren“. Intern hieß es dagegen: „Die eigenen Konstruktionen entsprechen nicht dem internationalen Stand der Technik. Sie sind Reparaturanfällig, erfordern einen zu großen Kraftbedarf und haben eine geringere Leistungsfähigkeit“.